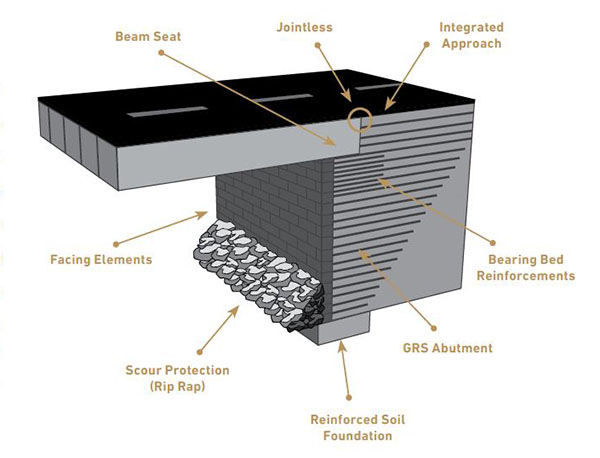
4 Types of Retaining Wall Construction
Retaining walls are a vital component of modern landscaping and infrastructure, providing essential support and aesthetic enhancements to projects. At Belgard, we specialize in four primary types of retaining walls, each offering unique benefits in terms of stability, durability, and design, allowing contractors to tailor solutions to their project’s specific needs. Explore the engineering principles and diverse applications behind these retaining wall systems to discover how Belgard products can bring unparalleled strength and beauty to your outdoor living spaces.
Gravity Wall Construction
A gravity retaining wall relies on the weight, depth, and batter of the SRW units to resist the soil forces exerted on the wall. Soil reinforcement is not used with gravity walls.
Gravity walls, using the smaller modular block systems, are suitable for residential projects, such as garden walls, low landscape walls, and decorative boundaries where space is limited. The allowable height of a gravity retaining wall is project-specific. It is typically limited to 2 to 3 times the front-to-back depth of the SRW-facing unit, making them ideal for applications where the desired wall height falls within these limits.
Whether used to create a gently graded lawn or to enhance the aesthetics of an outdoor space, gravity retaining walls using the smaller modular block systems offer a practical and visually appealing solution for managing elevation changes and preventing soil erosion.
Geosynthetic-Reinforced Retaining Wall
Geosynthetic reinforced walls use soil reinforcement layers, typically geogrids, to stabilize the soil behind the SRW facing, creating a coherent mass large enough to resist the soil forces acting on the wall system. The SRW facing unit, the geosynthetic reinforcement and the reinforced soil together then form the retaining wall system.
To resist more load, the reinforcement layers are lengthened and/or strengthened to provide the required resistance. Thus, reinforced wall systems can be designed for much taller earth retention heights and loading conditions than conventional gravity walls. Reinforced retaining walls should be designed by a qualified engineer and constructed by experienced contractors.
Mechanically Stabilized Earth Walls
Mechanically stabilized earth (MSE) walls offer a versatile and robust solution for various civil engineering and landscaping projects. These walls integrate reinforcing materials such as geogrids to enhance the structural stability of the soil, allowing for the construction of higher and more resilient retaining walls. The reinforcement provided by these materials effectively distributes loads and improves the overall performance of the wall, making them ideal for a range of applications. From highway embankments and bridge abutments to commercial developments and residential landscaping.
Mechanically Stabilized Earth Walls using Modular Block
MSE structures provide the strength and flexibility to adapt to diverse project needs. Their ability to support significant heights and withstand heavy loading conditions makes them a preferred choice for creating durable and aesthetically pleasing retaining structures.
Mechanically stabilized earth (MSE) walls use soil reinforcement layers, typically geogrids, to stabilize the soil behind the retaining wall facing, creating a coherent mass large enough to resist the soil forces acting on the wall system. The modular block facing unit, the geosynthetic reinforcement, and the reinforced soil form the retaining wall system.
To resist more load, reinforcement layers are added, lengthened, and/or strengthened to provide the required resistance. Thus, MSE wall systems can be designed for much taller earth retention heights and loading conditions than conventional gravity walls. MSE walls should be designed by a qualified engineer and constructed by experienced contractors.
Structural Backfill
Occasionally in retaining wall applications, enough space does not exist behind the face units to allow excavation for placement of geosynthetic reinforcement. For these instances, a gravity wall application can still be designed using specialized structural backfill to increase the depth and mass of the facing system. Using specialized structural backfill eliminates the use of geosynthetic reinforcement. The structural backfill also acts as the drainage zone for the retaining wall.
This design approach also requires substantially less excavation than required for MSE retaining walls. Retaining walls using structural backfill should be designed by a qualified engineer and built by experienced contractors. Structural backfill is also referred to as “no-fines concrete”, “stabilized aggregate”, and “Anchorplex System®”.
Geosynthetic Reinforced Soil–Integrated Bridge System (GRS-IBS)
The Federal Highway Administration has developed GRS-IBS technology as an innovative and cost-effective bridge system that is an alternative option to conventional bridge construction. The system uses closely spaced geosynthetic reinforcement layers and compacted aggregate to support the bridge superstructure.
Due to the simplicity of design, construction speed, use of readily available materials, and the elimination of deep foundations, the GRS-IBS method can reduce costs by 25-60% compared to conventional methods. GRS-IBS should be designed by a qualified engineer and constructed by experienced contractors.
A deep understanding of the various retaining wall types is essential for selecting the most appropriate solution for your landscaping or infrastructure project. Retaining walls play a critical role in ensuring stability and enhancing the aesthetics of outdoor spaces, whether for residential, commercial, industrial, or infrastructure applications. Each type of retaining wall offers unique benefits tailored to specific project needs, from managing soil pressure to accommodating significant height, and load requirements. By considering the strengths and applications of different retaining wall systems, contractors can achieve durable, visually appealing, and cost-effective results. Trust Belgard to provide the expertise and materials needed to transform your outdoor spaces with strong and reliable retaining wall solutions.
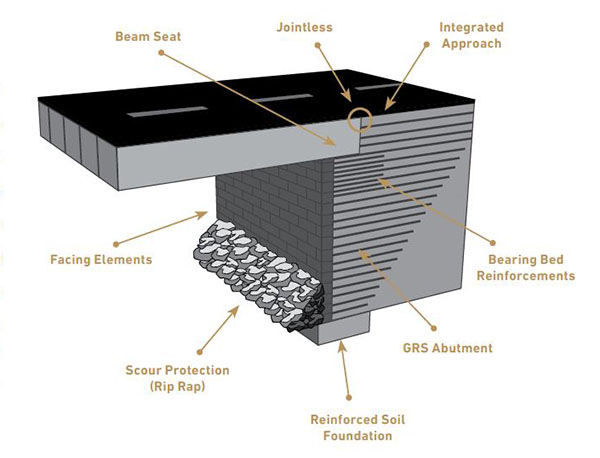